MaxinNews - interview poco Loco
2021/05/14
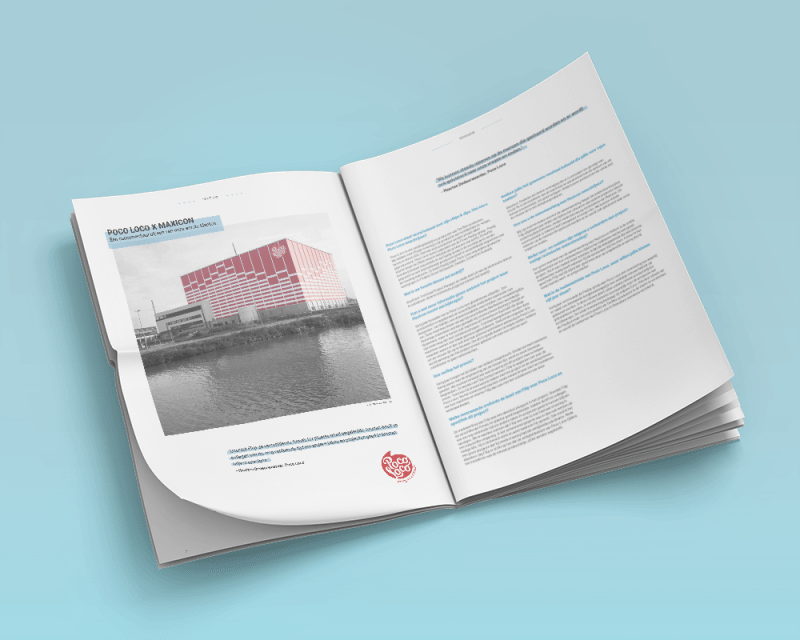
Poco Loco is known for its chips & dips. How would you describe Poco Loco?
Poco Loco is a food company and producer of Tex Mex products. We have over 20 years of experience in producing tortilla chips, tortillas and wraps, tacos and meal kits. There are two main departments we distinguish viz. frying & wraps. In the frying department, we make the tortilla chips. Today, we have 16 lines that produce the wraps every day.
Poco Loco is an international company. For instance, there is also a production site in the United Kingdom. In Belgium, we are only located in Roeselare, but our products go all over the world. Since 2010, Poco Loco has been part of the Paulig Group. A Finnish family business that has been around for 25 years. They are originally a coffee roasting company, but have expanded their group in recent years. A few years ago, Poco Loco was included in the group.
What is your position within the company?
I myself am Technical Project Manager within Poco Loco and am part of the technical department. I help coordinate all technical projects within the company.
Can you give some more information about the project Maxicon was allowed to contribute to?
The project involved the installation of a new chip line. Within such a line, you always have the components of the mixer and the baking line. For these machines, we work with different manufacturers. The parts come from all over the world. Some parts come from neighbouring countries like the Netherlands. They can easily supply and install them. But there are also installations that come from America and Australia. These goods take a long time to arrive by container ships. Normally, they send someone along to handle the installation, but covid-19 made this impossible. Hence, it became necessary for us to hire external technical staff and someone to manage this project.
How did the process go?
Last year, we were sent the brochure from Xellent. With the start-up of the new production line in mind, our interest was piqued. We were looking for someone with experience to steer this project in the right direction. That's how we got to know Filip, who started up just before the summer. Then he was able to get to know the workings within Poco Loco and soak up the atmosphere. After his leave, he could jump straight in and did just that.
What added value did Filip's efforts create for Poco Loco and specifically this project?
Filip definitely added value. I won't say that it wouldn't have been possible without him, but he did help us a lot. If we were to do the project again, we would definitely call on Filip again.
We immediately saw that he is a man with experience. In the exploratory meeting, we immediately clicked. He is technically strong and knows what he is talking about. His safety training was also a big plus. Because of his good approach, we gave him full confidence to lead the project independently after a few weeks. He drew up the schedule, directed the technicians and also took charge of communication in addition to daily follow-up.
Did you achieve the desired result you envisaged?
Looking back, everything actually went smoothly. Only the Covid-19 outbreak caused us a slight delay. Since we are a food company, we were fortunately allowed to continue working during the first wave. Thus, the delay did not exceed a few weeks.
How would you describe the cooperation with Maxicon?
We are very satisfied with the cooperation. Both for the project with Filip and with the technicians. Every Saturday, some external employees lend a hand with the maintenance of our machines. Communication is always very transparent and runs smoothly. We can always count on the people who are sent and our questions/needs are listened to.
What advantages and disadvantages do you see in project-based technical support?
A big advantage for us is the rapid deployment during busy periods. If I have to mention a disadvantage, it is the break-in period. Unlike working with our own people, new employees have to be trained all the time and cannot immediately pay off on the shop floor.
What is Poco Loco's vision for the future, where do you want to be within five years?
During the corona period, we saw an increase in sales of our tacos. Probably due to the closure of the catering industry. We hope this increase continues. In the middle of this year, we will start building a new production hall so as to add another line for our tortilla wraps. The new line will be located next to the existing production site in Roeselare. In this way, we want to strengthen our position as market leader in Europe and continue to innovate. The Paulig Group is also looking forward to international growth in countries such as England and Sweden.